Technological Realisations
The Savona
Combustion Laboratory (DIMSET/SCL) is located north of
the campus of the Savona School of Engineering, taking its
extension within two separate buildings: the right "wing"
of the Lab (devoted to liquid-fuel combustion systems, and
thus named "LF Area") occupies a 13 x 10 m2
masonry building, whilst on the left the Lab takes its
place within a 30.5 x 15.5 m2 hangar, mainly
dedicated to natural gas-fueled combustion systems testing
("NGF Area"). Both buildings, formerly of military
property, will progressively undergo a series of
structural and aesthetic restorations, while keeping
operativity (plant view of LF building, with the layout of the LRPM
burner test-rig, as well as the location of the Deutz
diesel engine utilised for electric power self-generation,
up to 150 kW). As of now, the electrical air-preheating
equipment of the burner
test-rig, absorbing about 110 kW so to reach 500°C at
full flow-rate, is fed by this latter power source. In a
near future, a 200 kW electric-power line will be
available. Closely outside of the LF building, a 2.0
m3 liquid-fuel store-tank is located, feeding,
under totally independent circuits, both the burner
test-rig and the diesel engine.
In the NGF hangar, a
natural-gas burner-testing furnace of 1000 kW
thermal-power is located, whilst a project is under
development for installing a mid-pressure (4 bar)
gas-turbine burner test-rig, fueled with natural gas and
possibly other gaseous fuels (syngas,
hydrogen).
As above said, in order
to experimentally test liquid fueled gas-turbine burners
of various typologies, and, more specifically,
premixer-burners of LRPM technology, a dedicated,
variable-geometry, atmospheric-pressure test-rig
(an isometric view of the overall test-rig), with an air
pre-heating electrical capability of up to about 500 °C,
has been designed, manufactured and erected in the LF
building (an isometric rendering of the Laboratory
with the remotely pc-controlled burner-rig installed in
the heat-shielded, fire-proof area of the Lab) of
DIMSET/SCL. In the same isometric view of the test-rig ,
the 3 electrical
preheaters (35 kW each) installed upstream of the
plenum chamber and the 9 traversing-stations locations
provided along the combustor length for reactive-flow
sampling are visible, as well as the water-jacketed
vertical discharge duct, leading the exhaust gasses up
to the outside stack, above the building roof.
Since the LRPM strategy
is basically rooted on physical principles, mainly of
fluid-dynamical (more than thermo-chemical) nature, it is
expected that, once satisfied the geometry, temperature,
Reynolds and Mach number similarities, together with a
reasonably sound interpretation of the parameters
governing spray-droplets behavior, the constraint of
atmospheric pressure for the test-rig will not sensibly
affect the validity of the experimental outcome and its
transposition to the actual operating pressure.
The radial-inflow LRPM
burner prototype (CAD sectional
drawings of the inward-radial-swirl LRPM burner
geometry) has been manufactured and installed, together
with its inner-duct axial-extension (30 mm length, 87 mm
i.d., of crucial importance for premixing process and
flame stability), in between the 400 mm i.d. plenum
chamber (for flow and temperature uniformisation) and the
150
mm i.d. combustor (25/35 Ni/Cr alloy, outer side
unshielded, inner side thermally coated). The design and
operational characteristics of the test rig are
synthetically shown in
Table 1 .
As above said, the
test-rig equipped with the LRPM premixer-burner is now
ready to undergo the first
pre-operational tests. Its instrumentation, in
addition to the classical optical pyrometry,
direct-sampling water-cooled traversing-probes (9
traversing stations along the combustor length) and
several wall-temperature monitoring-points (thermocouples)
already operational, will soon entail advanced laser-based
diagnostics. To this latter end, and always within the
frame of the MURST Program (Cluster 21) sponsoring this
research endeavor, a close cooperation is already planned
between DIMSET/SCL and ENEA, the Italian National Center
for Energy, in order to jointly proceed with the
application of advanced combustion-diagnostics
instrumentation to the experimental campaigns to be
performed on the test-rig here discussed.
Scientific Bases of LRPM
Strategy
In order to
attain the highly difficult target, for a liquid-fueled
gas-turbine combustor, of containing pollutant emissions
within one-digit-ppm limit, a peculiar strategy has been
followed and transferred into burner-design
technological-landmarks. The conceptual cornerstones which
the strategy is based on do not belong mainly to the
chemistry realm, rather they involve clear physical
principles of basic fluid-dynamical nature, in close
connection with two-phase flows and turbulence
theory.
The sequential reasoning
which motivates the LRPM strategy (for "Liquid-fuel Rapid
Pre-Mix") can be here synthesised as follows. In order to
achieve a strong containment of NOx emissions, flame
temperatures must be kept as low as possible, compatible
with flammability limits, whilst oxygen concentration must
be provided at high levels and at a well-mixed condition
(molecularly with fuel) in order to prevent CO production.
Whilst the flame temperature constraint can be tackled by
adoption of ultra-lean equivalence ratios, the core
problem, particularly with liquid fuels, is the attainment
of mixture’s molecular premixing, which, by its side,
pre-requires a rapid and complete vaporisation of the
liquid droplets.
The proposed solution to
this problem resorts to the intrinsic capacity of the
turbulence kinetic energy, for the larger scales, and,
more specifically for the smaller scales, of its
dissipation rate, to rapidly disaggregate the flow eddies
into ever smaller structures and then to "molecularly
diffuse" their residual dynamics into heat. If the burner
design could impose that, from a physical/fluid-dynamical
point of view, the turbulent kinetic energy and its
dissipation rate would be maintained, in localised
regions, at their maxima, then these regions (typically
represented by high-shear layers) could be selected as the
most suitable for "localised" injections of the liquid
fuel, thus providing a strong "drive" to its vaporisation
and turbulent mixing.
In addition, if, in
these regions, any recirculation of the flow could be
avoided by design, so to limit at a minimum the residence
times, then the overall process could, expectedly, enter
the "ultra low emissions" regime. Finally, if the
fuel-injection modality could maintain a well-defined,
directional, fuel-concentration gradient in the air shear
layer immediately ahead of the flame front, then the
combustion process will be free of thermo-acoustical
instabilities, typically related to non-directional
premixing modalities.
Theoretical Analysis and Design
Development
In order to refine and
support theoretically the LRPM burner design, with
specific reference to the crucial two-phase liquid-fuel
premixing process in presence of the counter-flow
influences (mass and heat convection, heat radiation,
possible thermo-acoustic perturbations, etc.) coming from
the flame process, a fully 3D time-dependent turbulent
reactive Navier-Stokes analysis has been performed by
applying, with parametric modalities, NastComb, the CRFD
("computational reactive fluid dynamics") Navier-Stokes
solver developed at DIMSET during the last 12 years
(Pittaluga, 1993; Pittaluga et al., 1994; Pittaluga
et al., June 1998; Pittaluga et al., Aug.
1998; Duranti & Pittaluga, 1997; Duranti &
Pittaluga, May 1999; Duranti & Pittaluga, 2000;
Luccoli et al., 1996; Luccoli et al., 1997;
Traverso, 2000). Since, under many respects, the design
activities, the technological developments, and even the
experimental testing, all pursued within the Savona
Combustion Laboratory, are closely interlinked with
parallel and complementary numerical analyses performed by
means of the said solver, a synthetic presentation of its
features, some of which are at all unique, is here deemed
important.
NastComb is the
combustive extension of Nast, a finite-volume, 3D, fully
time-dependent, turbulent, compressible
thermo-fluid-dynamical Navier-Stokes solver of ALE
(arbitrary lagrangian-eulerian) solution strategy, in
which every time-step consists of a lagrangian phase, with
the flow velocities applied to the (moving) grid vertexes
(
multi-block mesh-sector utilised for the
computations), followed by a convective phase, i.e. a
rezoning of the (updated) flow field, performed by
displacing the grid back to its initial position. A
monotone, nearly second-order (QSOU), differencing scheme
is applied for convection, with use of cell-face
velocities in order to lower numerical diffusion. To
increase numerical efficiency, a pressure-gradient scaling
(PGS) algorithm is activated whenever flow velocities are
particularly low. Grid types are staggered, boundary
fitted, multi-block, with hexahedroidal cells (Duranti
& Pittaluga, 1997).
The governing equations
for 3D, fully time-dependent, turbulent, variable-density,
reactive flow, in presence of conduction and radiation,
formerly of favre-average formulation, have recently been
converted into ensemble-average form (Duranti &
Pittaluga, 2000), in order to take full advantage of the
Markovian revisitation performed on its turbulence model.
This latter, developed and validated along several years,
is a three-equation, non-linear eddy-viscosity approach
based on the so-called "two-scale direct-interaction
approximation" (TSDIA) with a Markovian simplification
(MTS) for the solution of the approximate equations for
fluctuations (Duranti & Pittaluga, May 1999). The
model accounts for variable-density effects via a
transport equation for the density-variance, which
corrects the eddy-viscosity, and is thus particularly
suited to track the interactions between turbulence and
the density variations as induced by the reactive
field.
Combustion simulation is
performed following a "partial-equilibrium" approach,
whereby all reactions are pre-partitioned in two groups,
the "slow" ones, which proceed kinetically (Arrhenius
kinetics assumed), and the "fast" reactions, assumed in
equilibrium at all times. Both global schemes (Duranti
et al., May 2000) and quasi-global,
partial-oxidation, schemes (Pittaluga, 1994; Luccoli et
al., 1997) have been developed. On the other side, in
order to more correctly "detail" these schemes, a limited
set (12 to 16) of elementary reactions is anyhow adjoint
and programmed. In addition to fuel (gas or liquid), the
species considered are, typically, the following:
O2, O, CO, CO2, H2,
H2O, H, OH, N2, N, NO. A detailed
chemistry, parallel/clusterised version of NastComb is
under development, taking advantage of financial
sponsorships from MURST (co-financed national-interest
program) as well as the European Commission (ICLEAC
Program).
In order to take care of
turbulence effects, the expression of the total combustion
time t c is evaluated in Nastcomb as the sum of
a molecular time-scale t 1 (the inverse of
either the global or the quasi-global reaction rate,
according to the scheme adopted) and a turbulent
time-scale tt (related to the eddy turnover
time):
= + f 
where the delay
coefficient f , aimed at further correcting (i.e.
"delaying") the implications of reaction completeness
induced by the global assumption (if adopted), has been
assigned the expression :
f = ( 1 – e –r )/
0.632
where r is the
local ratio of the mass of products to that of total
reactive species (Duranti et al., May 2000). Of
course, to f a unit value is assigned when no
assumption of reaction completeness is implied, i.e. when
the overall reaction is of quasi-global type
(partial-oxidation).
For liquid fuels, the
treatment of fuel spray dynamics in NastComb is based on a
Monte Carlo method and adopts the concept of "discrete
particles". Strategy is that of sampling randomly from
assumed probability distributions that govern droplet
properties at injection and droplet behavior subsequent to
injection. Turbulent correlation times associated with
proper distributions of turbulent displacements for spray
droplets are considered. The stochastic particle method is
suitable to calculate evaporating liquid sprays including
the effect of droplet collisions, coalescence and
aerodynamic breakups (secondary atomisation) (Duranti
et al., May 2000).
In Nastcomb solver a
detailed, non-equilibrium, continuous-field,
time-dependent 3D radiation model has been introduced, and
made interactive with the overall turbulent reactive
thermo-fluid-dynamical solution. Originally the model, of
a "neutronic" character, was developed within a 2D,
equilibrium assumption for the radiation diffusion
treatment. Then, the scheme has been extended to
nonequilibrium diffusion, wherein the gas and the
radiation fields can have different temperatures, and
flux-limiters are adopted to extend the diffusion theory
to optically-thin regions, with also 3D capability
(Pittaluga et al., 1998; Duranti et al.,
2000). In synthesis, the transport equation for the
radiation energy-density is solved fully coupled with the
gas energy-density equation. The coupling terms which
relate the radiation energy density to the fluid energy
density are large when the photon mean-free paths due to
molecular collisions are small ("optically-thick" regions)
whilst the opposite is true in "optically thin"
regions.
At the end of the
computations can be obtained predictions of the turbulent
kinetic energy, its dissipation
rate, pressure
and temperature
distributions in a meridian plane of the combustor. The
solution is fully 3D and reactive. Notice that the picture
changes for different meridian planes, in particular for
the k and e distributions, which gives extremely important
information about the correct azymuthal orientation of
fuel injection holes, in order, for the spray droplets, to
attain exactly into the dissipation rate peaks.
Finally it also can be
seen a perspective internal view is given of the burner-combustor
assembly with the eight-vane radial-inflow premixer:
the flow is from bottom to top. The liquid fuel
(typically: "jet-A" for aero-propulsion applications, or
"distillate #2" for heavy-duty gas turbines) is injected
either radially inward, within each one of the 8
vane-channels or, alternatively, directly from the
premixer "eye", on the burner centerline. In this latter
case, the fuel is introduced by means of an eight-faceted
conical injector, provided with one 0.4 mm injecton hole
for each (locally planar) facet, with an injection-path
azymuthal setting and meridian-plane orientation suitable
to attain exactly into the shear layers produced by the
radial vanes.
Outcome of Performance Testing
In order to experimentally test liquid fueled gas-turbine
burners of various typologies, and, more specifically, premixer-burners of
LRPM technology, a dedicated, variable-geometry, atmospheric-pressure
test-rig, with air pre-heating electrical capability of up to about 500 °C, has
been designed, erected and made fully operative in a dedicated wing of SCL
Laboratory. Since LRPM strategy is basically rooted on physical principles,
mainly of fluid-dynamical (more than thermo-chemical) nature, it is
expected that, once satisfied dimensional, temperature, Reynolds and Mach
number similarities, together with a reasonably sound interpretation of the
parameters governing spray-droplets behavior, the constraint of atmospheric
pressure for the test-rig will not sensibly affect the validity of the
experimental outcome and its transposition to the real-duty pressure.
In order to experimentally test liquid fueled gas-turbine
burners of various typologies, and, more specifically, premixer-burners of
LRPM technology, a dedicated, variable-geometry, atmospheric-pressure
test-rig, with air pre-heating electrical capability of up to about 500 °C, has
been designed, erected and made fully operative in a dedicated wing of SCL
Laboratory. Since LRPM strategy is basically rooted on physical principles,
mainly of fluid-dynamical (more than thermo-chemical) nature, it is
expected that, once satisfied dimensional, temperature, Reynolds and Mach
number similarities, together with a reasonably sound interpretation of the
parameters governing spray-droplets behavior, the constraint of atmospheric
pressure for the test-rig will not sensibly affect the validity of the
experimental outcome and its transposition to the real-duty pressure.
A picture of the LRPM burner test-rig is given in Figure 1. In the same
Figure, the 3 electrical preheaters (35 kW each) installed upstream of the
plenum chamber are visible, as well as the water-jacketed vertical discharge
duct, leading the exhaust gasses up to the outside stack, above the building
roof.
The main characteristics of the test-rig are reported in Table 1.
Starting from about one year ago, a series of experimental campaigns have
been performed in order to directly assess the validity of the LRPM concept,
above discussed from a theoretical point of view. Thanks to the cooperation
with ENEA, the Italian National Center for Clean Energy, it has become
possible to jointly proceed with the application of advanced combustion
instrumentation, with the aim of achieving a series of reliable and detailed
diagnostic pictures, particularly in connection with the flame process characterisation, the emissions assessment and the combustion stability analysis.
In order to assess the flame process characteristics within the combustor, it
is crucial to achieve a map of the temperatures within the combustion
chamber. To this end, in addition to the 8 "skin-point" thermocouples
provided on the walls of the combustor, along its axial length, a special 5-
probe combined-thermocouple has been utilised, expressly designed and
manufactured for this application. In order to sustain flame temperatures up
to 1700 °C, it is made completely in ceramics (no metal parts inside), with
fully embedded probe-wiring, which thus turns out highly shielded from the
outside. It is pictured in Figure 2, whereas Figure 3 shows its introduction
holes provided into the combustor walls. Notice that as many holes, with
displaced locations, are also provided on the diametrically opposite wall.
Figure 5 presents the experimental temperature distribution, compared with
NastComb's predictions: the comparison turns out satisfactory, some times
rather good. Notice the absence of peak temperatures above 1350 °C and a
very smooth temperature distribution in the whole chamber, confirming
attainment of adequate premixing levels ahead of the flame front.
On the other hand, a careful analysis of the exhaust gasses is mandatory in
order to check the achievement of the ultra-low emission regime, in terms of
NOx and CO. To this end, the combustion gasses are sampled about 1.5 m
duct-length downstream of the combustor, after the exhaust cooling section,
in a location where the recombination processes should be largely attained.
The exhaust gasses of the combustor are analysed by means of two
different diagnostic instruments, namely, a Chemical Ionization Mass
Spectrometer (Airsense 500) and a Fourier Transform Infrared Spectroscope
(FTIR). The first instrument is based on an ionization system with charge
exchange. It yields the qualitative and quantitative determination of the
molecular components of the exhaust gasses, operating in real time (Tmin = 1
ms) and with a very high resolution (0.001 ppm). The FTIR instrument is
based on the characteristic absorption of the infrared radiation by the
different chemical species, allowing to measure up to 12 different species
simultaneously. It is characterised by high stability and easy calibration, thus
assuring a very simple and quick utilisation.
The CO and NOx emission trend measured as a function of the preheating
temperature of the air is presented in Figure 6. Notice the full attainment of
the ultra-low regime, a very important result, particularly in connection with
a liquid fuel such as gas-oil. Notice also that the NOx emission levels are
throughout very low and that, quite importantly, they decrease by lowering
the preheated air temperature, thus limiting the thermal NOx production.
This shows that the attainment of a good premixed condition has been
satisfied for the whole range of preheating temperatures, with the additional
evidence that the said condition is achieved not by thermo-dynamical means
(i.e. increase of temperature, enhancing droplet vaporisation), rather, thanks
to fluid-dynamical reasons (i.e. turbulence-controlled process).
Notice how clearly, from a perspective of emissions' control, the optimised
operational characteristics of the burner can be definitely assessed from
Figure 6. Actually, thermal NOx is steadily decreasing with the decrease of
the air preheating temperatures. On the other hand, CO emissions are almost
constant until the air temperature gets lower than about 340 °C. Thus, the
latter condition turns out as the most suitable to limit to an extremely low
level the environmental impact of the combustion system. Notice also that
the emissions levels shown throughout Figure 6, and not just at the optimal
point, are amply contained within the ultra-low emissions range for gasoil.
Finally, in order to experimentally investigate the stability characteristics
of the LRPM burner, in particular connection with its thermo-acoustical
stability, in addition to the adoption of classical pressure transducers, an
innovative detection technique has been developed and successfully applied,
now subject to become patented. The technique is based on digital optics and
employs a digital camera (Dalsa CA-D1, 128x128, 736 frames/s) that, at a
high speed, takes and collects images of the flame process (Figure 7).
The images are, in real time, elaborated by a specialised software that
evaluates the flame brightness gradient (first-order time-derivative). By
performing a fourier transform on these data, the characteristic frequency of
the light fluctuation is obtained. Interestingly, this frequency turns out
exactly the same as that of the pressure oscillations. It is thus correct to
analyse the combustion instability by adopting this digital/optical technique
which appears suitable not just to detect the actual presence of instability
pulsations, as is the case of the pressure transducers, but also of predicting
their occurrence with an advance-time of the order of one second, to the
advantage of a control action preventing the instability to occur.
Other Photos
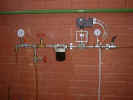
|